
In-depth discussion of the design concept, functional characteristics and application scenarios of the sleeve to understand how it has become an indispensable tool in maintenance and assembly work.
Basic concepts of the sleeve
Sleeve is a common hand tool, mainly used to tighten or loosen nuts and bolts. Its history can be traced back to the end of the 19th century. With the development of the industrial revolution, the sleeve gradually became an essential tool in maintenance and assembly work.
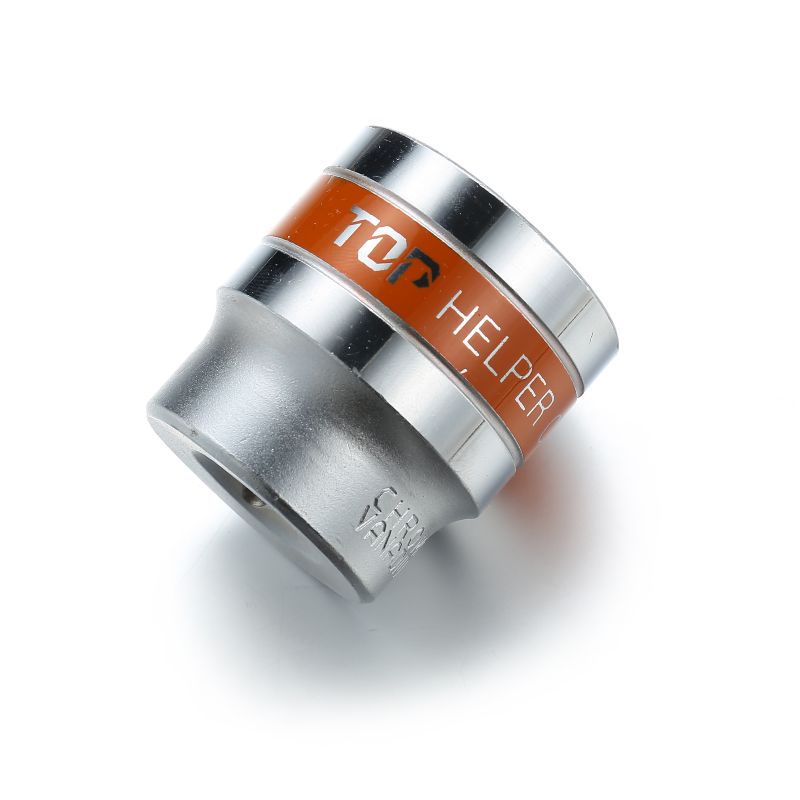
What is a sleeve
The socket is usually made of high-quality steel, and the shape is mostly hexagonal or dodecagonal. It can be used with wrenches, ratchets or other tools to more easily complete work tasks.
The history and development of the sleeve
The earliest sleeves appeared in the late 19th century, when industrial production increased the demand for tools. Over time, the design of the sleeve continued to improve, from simple hand-made to modern high-precision manufacturing processes.
Classification of sleeves
According to the different driving methods, the sleeve is mainly divided into three types: manual sleeve, electric sleeve and pneumatic sleeve.
Manual Sleeve
Manual sleeves are the most common type and are suitable for most household and small maintenance tasks. They are portable and easy to carry, easy to use.
Electric Sleeve
The electric sleeve is suitable for tasks that require a lot of torque, such as automobile maintenance and heavy machinery assembly. They provide strong power support and save manpower.
Pneumatic Sleeve
Pneumatic sleeves are driven by compressed air and are commonly used in industrial production lines and large maintenance operations. They have the characteristics of high efficiency and long life.
Sleeve design concept
Excellent sleeve design must not only consider practicality, but also focus on ergonomics, durability and versatility.
Ergonomic Design
The handle design of the sleeve conforms to the ergonomic principle, ensuring that you will not feel tired after long-term use. Reasonable weight distribution and non-slip surface treatment make it more comfortable and safe.
Durability and reliability
The high quality steel and advanced heat treatment process make the sleeve have excellent wear and impact resistance, and it can be used for a long time even in harsh environments.
Versatility
The sleeve is usually equipped with a variety of specifications, which can be flexibly selected according to different work requirements. Some high-end models are also equipped with a torque adjustment function that ensures precise operation.
Functional features of the sleeve
The reason why the sleeve has become an essential tool for maintenance and assembly work is closely related to its unique functional characteristics.
Quick disassembly
The quick connection design of the sleeve makes it very convenient to replace the sleeve, saving a lot of time and labor.
Torque adjustment
Some sleeves are equipped with a torque adjustment function, which can adjust the appropriate torque according to different work requirements to prevent over-tightening or over-loosening.
A variety of specifications to meet different needs
The sleeve usually provides a variety of specifications of the insert, from small screws to large-diameter nuts can cope with ease, to meet the needs of different scenarios.
Application scenario of the sleeve
Sleeve is widely used in various fields because of its versatility and reliability.
Home Maintenance
In the maintenance process of household appliances and furniture, the sleeve can help you easily solve various problems, such as tightening screws, replacing parts, etc.
Car Repair
In car maintenance, the sleeve is one of the essential tools. Whether it is changing tires, repairing the engine or adjusting the chassis, the sleeve can play an important role.
Industrial Assembly
In industrial production lines, sleeves are used to assemble and disassemble various mechanical equipment to ensure the normal operation of the production line.
Building Construction
In the construction, the sleeve is used to fix the steel structure and install the pipeline to ensure the safety and stability of the building.
How to choose the right sleeve
There are many types of sleeves on the market. How to choose the product that best suits your needs? Here are some suggestions.
Select type according to job requirements
If you are mainly engaged in home maintenance, manual sleeves may be a good choice; if it is car maintenance or industrial assembly, it is recommended to choose electric or pneumatic sleeves.
Considering material and strength
High-quality steel and advanced manufacturing technology can ensure the durability and reliability of the sleeve. When selecting, pay attention to the material description and technical parameters of the product.
Brand and after-sales service
Choose well-known brand products, you can enjoy better quality and after-sales service. Before buying, you can consult relevant reviews and user feedback, and choose brands with good reputation.
Maintenance of sleeve
Correct maintenance and maintenance of the sleeve can extend its service life and ensure that it is always in the best condition.
Daily Cleaning and Lubrication
After each use, the dirt and dust on the sleeve should be cleaned in time, and an appropriate amount of lubricating oil should be applied to prevent rust.
Periodic inspection and replacement
Regularly check the sleeve for cracks or deformation. If there is any abnormality, it should be replaced in time to avoid affecting the use effect.
Storage Considerations
Store the sleeve in a dry and ventilated place, avoid contact with corrosive substances, and keep away from high temperature and humid environment.
How to use the sleeve
Mastering the correct use skills can make the sleeve play a greater role.
Correct grip
When holding the handle of the sleeve, the fingers should be close to the handle with even force to avoid accidental injury caused by slippage.
Reasonable force application method
When applying force, it should be along the axis to avoid lateral force, which can reduce the wear of the sleeve and extend the service life.
Avoid misuse and damage
Do not use the sleeve as a crowbar or other non-designated purposes to avoid damage to tools or cause safety accidents.